Bulk Material Chain Plate Belt Composite Apron Feeder
Application Case of Bulk Material Chain Plate Belt Composite Feeder
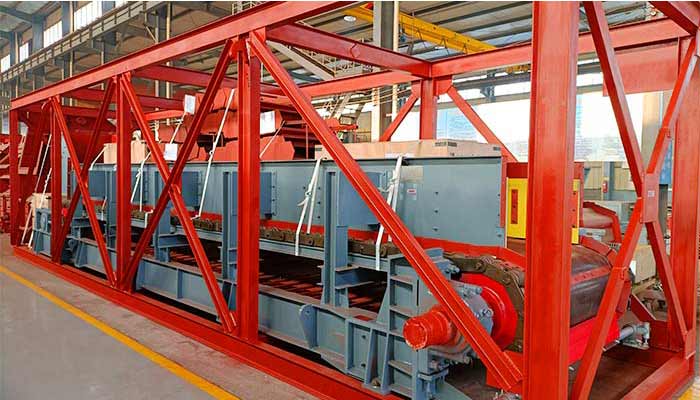
Project Overview
In a 30MW-class biomass power plant, the efficient conveyance of diverse biomass materials to meet boiler requirements posed significant challenges. The material mix included agricultural straws, branches, forestry straws, rice husks, and both processed/unprocessed straws, each with distinct physical properties. To address material blockages, uneven feeding, and handling inconsistencies, a specially customized Bulk Material Chain Plate Belt Composite Feeder was designed and deployed.
Customized Equipment Design & Key Features
Engineered to the power plant's unique needs, this feeder integrates the advantages of chain plate and belt conveying systems:
- Dual-mode Conveyance: Combines robust chain plate strength for heavy/slightly abrasive materials with belt flexibility for lighter, fluffy biomass, enabling continuous, adjustable material transportation.
- Material Adaptability: Customized to handle varied shapes (whole straws, crushed particles) and densities (300–600 kg/m³), ensuring seamless operation with mixed lightweight (rice husks) and moderately heavy (branches) materials.
Application Scope & Material Handling Capabilities
Industrial Applicability
The feeder serves multiple industries, including:
- Biomass Power Generation (primary application here)
- Food Processing for high-volume material transportation
Specific Material Handling in the Power Plant
Conveyed Materials:
- Primary Materials: Agricultural straws, branches, forestry straws, and minor rice husks.
- Gray Straws: Pre-processed before factory entry, all particles < 100mm.
- Yellow Straws: Mostly in original form (unprocessed whole stalks).
- Restricted Materials: No hard objects > 30kg allowed to prevent equipment damage.
Density Specifications:
- High-bulk-density Mixtures: Wood, charcoal, cotton straws, and their crushed blends have a bulk density of 300–350 kg/m³.
- Wet Cotton Straws: Highly absorbent, with a wet bulk density up to 600 kg/m³; only minimal quantities (minor blending) are permitted in the material mix to maintain optimal feeding performance.
Operational Performance & Outcomes
Since installation, the customized feeder has delivered transformative results:
- Stable Material Supply: Continuous, adjustable feeding ensures consistent boiler fuel input, eliminating previous issues of blockages and uneven distribution.
- Enhanced Efficiency: Seamless handling of mixed materials improves overall plant operational efficiency, reducing downtime caused by material-related disruptions.
- Cost Optimization: The tailored design minimizes maintenance needs and extends equipment lifespan, lowering long-term operational costs.
- Sustainability Impact: Reliable material conveyance supports the plant's increased capacity to convert biomass into clean energy, advancing sustainable power generation goals.
This case demonstrates how a bespoke Bulk Material Chain Plate Belt Composite Feeder addresses the unique challenges of biomass power plants, combining technical innovation with material specificity to achieve operational excellence.